We didn't get a particularly early start, but since the place is only 170 miles away we were only looking at a one hour flight time. The weather was good for flying cross country, with glass smooth skies above 3,500' and a nice overcast at 25,000'. Bright blue skies are nice to look at, but the sun coming through the bubble-like canopy of the RV-6 can really heat things up so a little overcast is beneficial on longer trips.
I usually monitor the destination airport's unicom frequency while still many miles out, and today that turned out to be particularly helpful. While we were in our descent into the landing pattern in PA, I heard a position announcement from Grove City Skydive, alerting all local traffic (i.e. us) that he was going to drop jumpers in 5 minutes. A quick glance at the GPS showed us arriving over the airport in 4:45 minutes. Well, there was a poser. I've never had this happen before, but I'm pretty certain that the jumpers would have the right-of-way, and even if they didn't, hitting one of them is usually fatal for all involved. Luckily, the pilot of the jump plane seemed very experienced and worked with me on the radio to ensure that we didn't suffer an untoward airborne rendezvous with a parachuter.
The ensuing landing was complicated by the downhill sloping runway but was fairly decent. At least the critical observer in the co-pilot seat didn't have anything derogatory to say about it, and that's a 'win' in my book. We were met at the plane with a friendly guy bearing the gift of chocks, but at $4.25/gallon I had to decline the proffered fill-up. After a quick (and very welcome! The bumpy air on arrival, combined with the 32 ounces of coffee inhabiting my 24 ounce bladder, had exacerbated my enroute discomfort quite startlingly) restroom break, we started the trek to the mall.
The mall is actually pretty close to the airport.
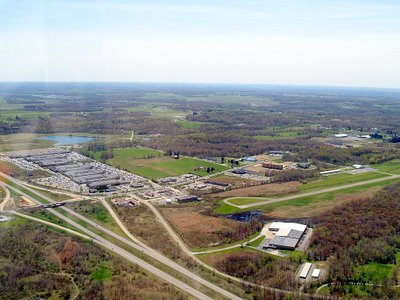
Had we not stopped at Wendy's, it would have been no more than a 15 minute walk. I wasn't thrilled with the choice of Wendy's, but it was the co-pilot's turn to chose. I would have preferred to try the nice looking pub/restaurant right next door.
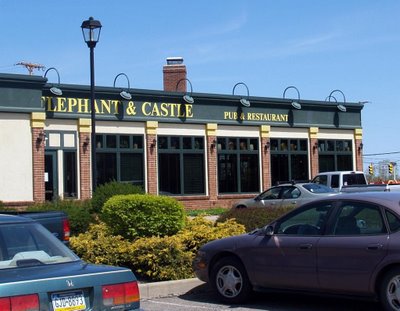
The mall is quite large and attractively landscaped.
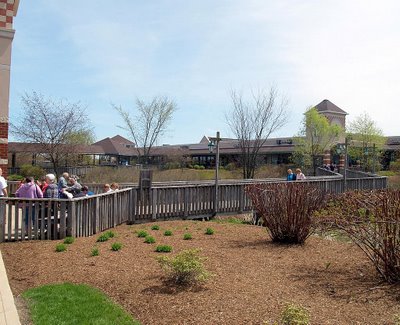
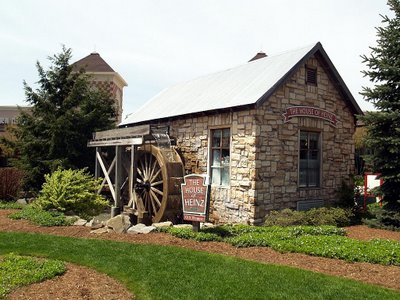
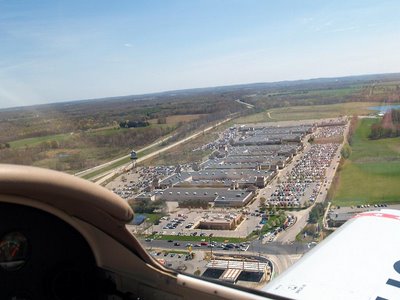
The stores have Kohls-like prices at worst, and I'm sure plenty of even more deeply discounted items are available. The contrast with mall prices for the very same merchandise is striking, but compared with Sams Club or Kohl's the outlet mall is only slightly better on prices. The selections, however, are obviously far broader. I picked up a few work shirts, and co-pilot Egg gravited to the "girly" stores where she could try on cosmetics and fragrances.
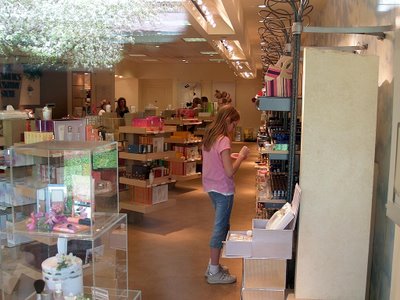
I had to insist on keeping the perfume samples to an absolute minimum, though, knowing very well what it would be like to spend a hot, bumpy hour flying home with her if she had free rein to spritz to her hearts content.
We climbed to 6,500' for the trip back, and it wasn't until we were over 5000 that the air smoothed out again. The overcast had grown thicker and gotten lower than our trip out, but at 12,000' was still high enough not to impede our progress. We'll probably have storms tomorrow, though.
I decided since we were high enough to just go right over Columbus instead of making the detour all the way around their airspace, which saves at least 15 minutes of flying time, and is a bit more scenic.
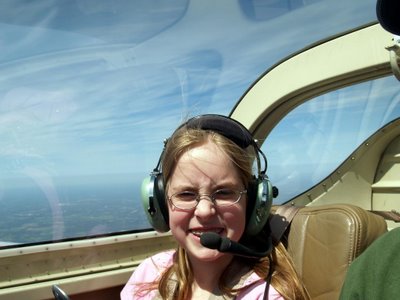
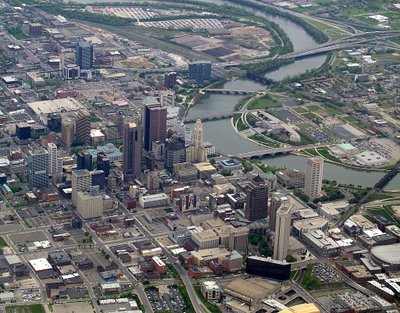
The controllers held us at 5,500' until we were well south of the approach path to the east-facing runways at Port Columbus, so we were within 8 miles of Bolton before I was allowed to descend. That's really not a problem in the RV, though. She comes down like a brick if you want her too. We hit left downwind to runway 4 doing about 140 knots, but my draggy plane easily slowed to flaps extension speed (100 mph) well in time for the turn to the base leg. The wind had picked up a but since we left, but was still only 8 knots or so, albeit a direct crosswind. I share these esoteric details mostly in excuse for my not-so-great landing.
Lot's of bugs to wipe off today. People are often surprised when I tell them that even at altitudes higher than 6,000' I still hit bugs. I saw one splatter on the windshield right in front of me today at 6,500'! Damned over-achievers.